PORTFÓLIO
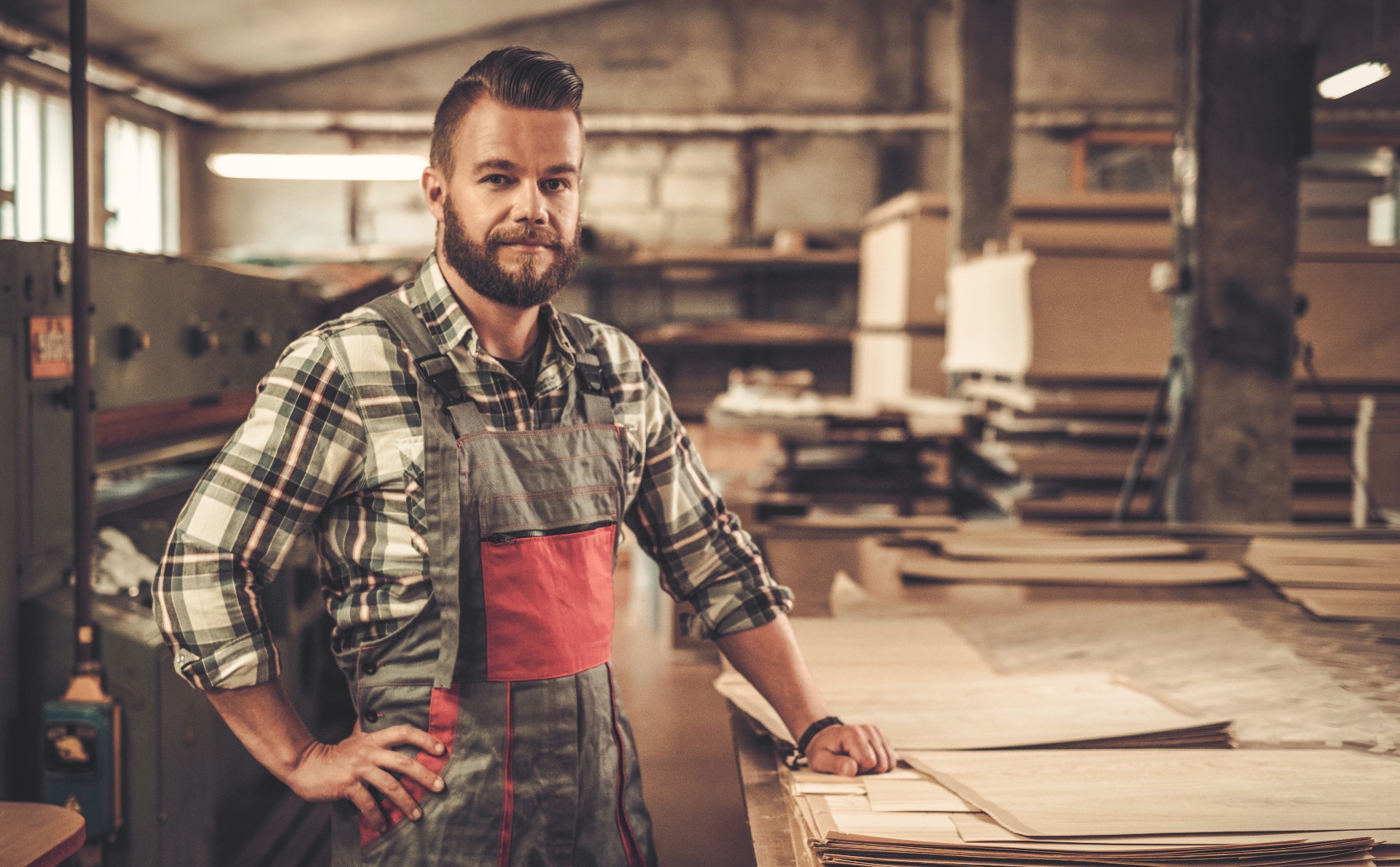
1 - Apreciação de riscos
Apreciação de Riscos conforme NR 12 e ABNT NBR ISO 12100
A apreciação de riscos é um processo essencial na análise e gestão de segurança em ambientes industriais, principalmente na operação de máquinas e equipamentos. No Brasil, a Norma Regulamentadora NR 12 e a norma internacional ABNT NBR ISO 12100 são referências fundamentais para essa prática.
NR 12 - Segurança no Trabalho em Máquinas e Equipamentos
A NR 12 estabelece requisitos mínimos para a prevenção de acidentes e doenças do trabalho em máquinas e equipamentos. Ela abrange aspectos como:
- Conscientização e treinamento: Garantir que os trabalhadores sejam devidamente informados e treinados sobre os riscos associados às máquinas.
- Proteções físicas: Implementação de barreiras físicas, dispositivos de segurança e sinalizações adequadas para prevenir o contato direto com partes perigosas.
- Manutenção e inspeção: Realização de manutenção regular e inspeções para garantir que as máquinas estejam em condições seguras de operação.
- Documentação e registros: Manter registros detalhados de avaliações de riscos, treinamentos realizados e manutenção das máquinas.
ABNT NBR ISO 12100 - Princípios para o Projeto e Avaliação de Máquinas
A ABNT NBR ISO 12100 fornece diretrizes para o projeto e avaliação de máquinas, com foco na segurança. Ela é composta por três etapas principais:
- Identificação de perigos: Identificar todos os perigos potenciais associados ao uso da máquina.
- Estimativa de riscos: Avaliar a probabilidade e a gravidade dos danos potenciais, utilizando métodos como a Análise de Risco por Nível de Risco (HRN).
- Avaliação de riscos: Determinar se o risco é aceitável ou se medidas adicionais de controle são necessárias.
Método HRN (Hazard Rating Number)
O método HRN é uma ferramenta utilizada para quantificar os riscos associados a perigos identificados. Ele considera os seguintes fatores:
- Gravidade do dano (S): Impacto potencial caso o perigo se materialize.
- Probabilidade de ocorrência (P): Frequência com que o perigo pode ocorrer.
- Possibilidade de evitar o dano (A): Capacidade de evitar ou mitigar o impacto.
- Exposição ao perigo (E): Quantidade de tempo em que o trabalhador está exposto ao perigo.
A fórmula para calcular o HRN é:
HRN = GS x FE x PO x NP
Com base no valor obtido, os riscos são classificados e priorizados para a implementação de medidas de controle.
Importância da Apreciação de Riscos
A realização adequada da apreciação de riscos conforme a NR 12 e a ABNT NBR ISO 12100 é crucial para garantir a segurança dos trabalhadores. Ela ajuda as empresas a criar um ambiente de trabalho mais seguro, reduzindo a probabilidade de acidentes e promovendo uma cultura de segurança contínua. Além disso, contribui para o cumprimento das obrigações legais e normativas, evitando penalidades e melhorando a imagem corporativa.
Conclusão
A apreciação de riscos é uma prática essencial na gestão de segurança ocupacional. Através da aplicação das diretrizes da NR 12 e da ABNT NBR ISO 12100, as empresas podem proteger seus colaboradores de forma eficaz, garantindo um ambiente de trabalho seguro e produtivo.
1 - Apreciação de riscos
Apreciação de Riscos conforme NR 12 e ABNT NBR ISO 12100
A apreciação de riscos é um processo essencial na análise e gestão de segurança em ambientes industriais, principalmente na operação de máquinas e equipamentos. No Brasil, a Norma Regulamentadora NR 12 e a norma internacional ABNT NBR ISO 12100 são referências fundamentais para essa prática.
NR 12 - Segurança no Trabalho em Máquinas e Equipamentos
A NR 12 estabelece requisitos mínimos para a prevenção de acidentes e doenças do trabalho em máquinas e equipamentos. Ela abrange aspectos como:
- Conscientização e treinamento: Garantir que os trabalhadores sejam devidamente informados e treinados sobre os riscos associados às máquinas.
- Proteções físicas: Implementação de barreiras físicas, dispositivos de segurança e sinalizações adequadas para prevenir o contato direto com partes perigosas.
- Manutenção e inspeção: Realização de manutenção regular e inspeções para garantir que as máquinas estejam em condições seguras de operação.
- Documentação e registros: Manter registros detalhados de avaliações de riscos, treinamentos realizados e manutenção das máquinas.
ABNT NBR ISO 12100 - Princípios para o Projeto e Avaliação de Máquinas
A ABNT NBR ISO 12100 fornece diretrizes para o projeto e avaliação de máquinas, com foco na segurança. Ela é composta por três etapas principais:
- Identificação de perigos: Identificar todos os perigos potenciais associados ao uso da máquina.
- Estimativa de riscos: Avaliar a probabilidade e a gravidade dos danos potenciais, utilizando métodos como a Análise de Risco por Nível de Risco (HRN).
- Avaliação de riscos: Determinar se o risco é aceitável ou se medidas adicionais de controle são necessárias.
Método HRN (Hazard Rating Number)
O método HRN é uma ferramenta utilizada para quantificar os riscos associados a perigos identificados. Ele considera os seguintes fatores:
- Gravidade do dano (S): Impacto potencial caso o perigo se materialize.
- Probabilidade de ocorrência (P): Frequência com que o perigo pode ocorrer.
- Possibilidade de evitar o dano (A): Capacidade de evitar ou mitigar o impacto.
- Exposição ao perigo (E): Quantidade de tempo em que o trabalhador está exposto ao perigo.
A fórmula para calcular o HRN é:
HRN = GS x FE x PO x NP
Com base no valor obtido, os riscos são classificados e priorizados para a implementação de medidas de controle.
Importância da Apreciação de Riscos
A realização adequada da apreciação de riscos conforme a NR 12 e a ABNT NBR ISO 12100 é crucial para garantir a segurança dos trabalhadores. Ela ajuda as empresas a criar um ambiente de trabalho mais seguro, reduzindo a probabilidade de acidentes e promovendo uma cultura de segurança contínua. Além disso, contribui para o cumprimento das obrigações legais e normativas, evitando penalidades e melhorando a imagem corporativa.
Conclusão
A apreciação de riscos é uma prática essencial na gestão de segurança ocupacional. Através da aplicação das diretrizes da NR 12 e da ABNT NBR ISO 12100, as empresas podem proteger seus colaboradores de forma eficaz, garantindo um ambiente de trabalho seguro e produtivo.
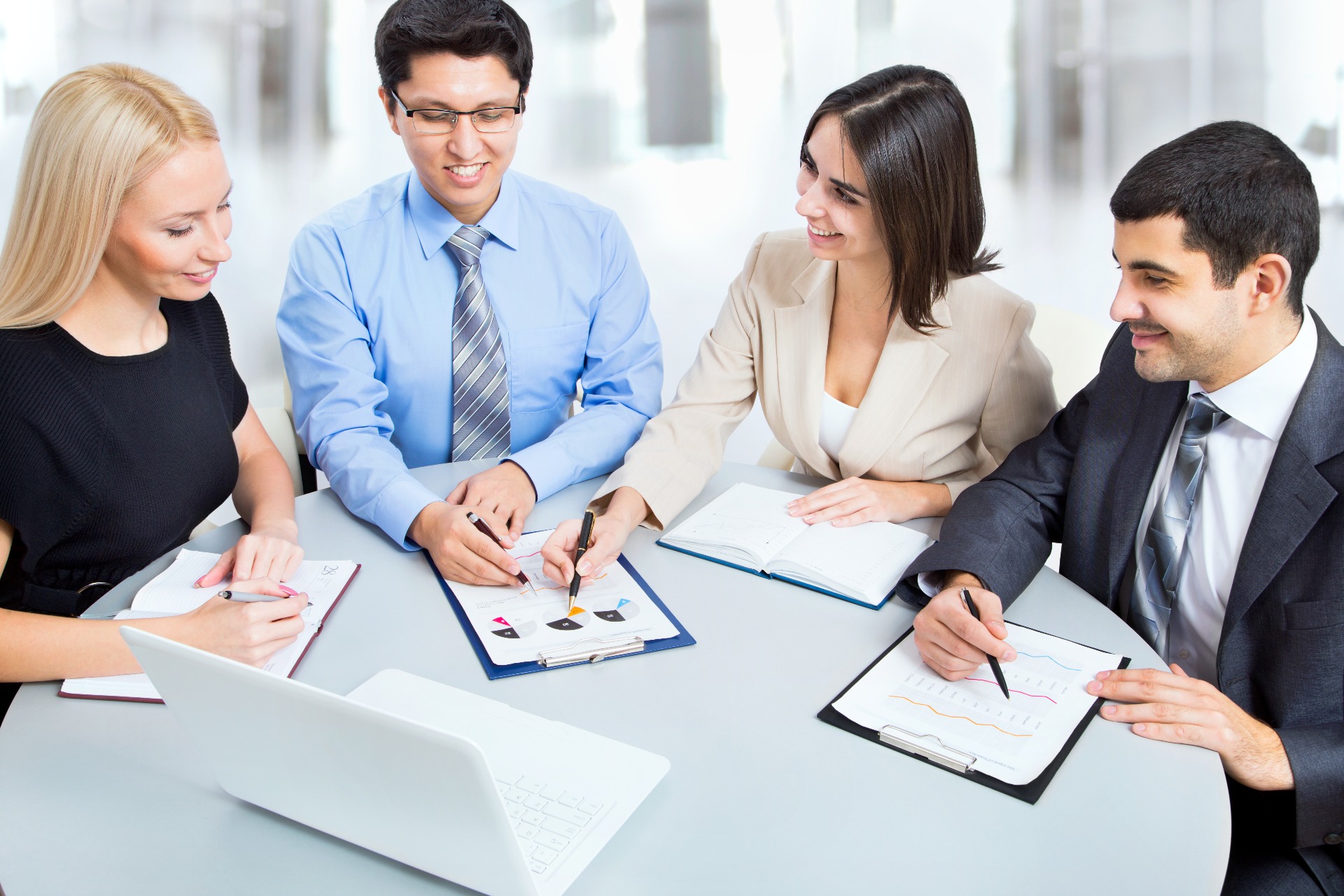
- Análise de Risco:
- Realização de análise de risco detalhada para identificar potenciais perigos associados a cada máquina.
- Implementação de medidas de controle conforme a criticidade dos riscos identificados.
- Proteções Físicas:
- Instalação de proteções fixas e móveis em pontos de acesso a partes móveis das máquinas.
- Verificação e adequação das barreiras de segurança e dispositivos de intertravamento.
- Dispositivos de Segurança:
- Inclusão de botões de emergência em locais estrategicamente posicionados.
- Implementação de sistemas de parada de emergência que atendam às exigências normativas.
- Sinalização:
- Colocação de placas de advertência e instruções de operação próximas aos equipamentos.
- Uso de cores e símbolos padronizados para facilitar a identificação de áreas de risco.
- Treinamento dos Trabalhadores:
- Realização de treinamentos periódicos para capacitar os trabalhadores sobre os procedimentos de segurança atualizados.
- Sessões de conscientização sobre a importância do uso de Equipamentos de Proteção Individual (EPIs).
- Manutenção Preventiva:
- Implementação de um plano de manutenção preventiva para garantir o funcionamento seguro e eficiente dos equipamentos.
- Registros detalhados das inspeções e manutenções realizadas.
- Proteções e Dispositivos: Todas as proteções instaladas estão em conformidade com as especificações normativas.
- Procedimentos de Segurança: As práticas de operação e manutenção seguem as diretrizes de segurança estabelecidas.
- Treinamento e Capacitação: Os trabalhadores demonstraram compreensão adequada dos procedimentos de segurança.
- Monitoramento Contínuo: Estabelecer um sistema de monitoramento contínuo para identificar e corrigir potenciais riscos futuros.
- Atualização de Treinamentos: Manter os programas de treinamento atualizados conforme novas normas e tecnologias sejam introduzidas.
- Revisão Periódica: Realizar revisões periódicas das medidas de segurança para garantir sua eficácia contínua.
2· Laudo de Conformidade
Laudo de Conformidade Pós Adequações à NR 12 e Normas Técnicas
Introdução
Este laudo tem como objetivo apresentar o resultado das adequações realizadas com base na Norma Regulamentadora 12 (NR 12) e nas normas técnicas aplicáveis, visando a mitigação dos riscos associados ao maquinário e equipamentos em operação. A NR 12 estabelece requisitos mínimos para a prevenção de acidentes e a promoção da segurança no ambiente de trabalho.
Descrição das Adequações Realizadas
Avaliação de Conformidade
Após a implementação das adequações, foi realizada uma inspeção minuciosa para avaliar a conformidade com a NR 12 e outras normas técnicas aplicáveis. Os seguintes aspectos foram considerados:
Conclusão
As adequações realizadas resultaram em um ambiente de trabalho mais seguro e em conformidade com a NR 12 e normas técnicas vigentes. A mitigação dos riscos foi alcançada através de medidas eficazes, garantindo a segurança dos trabalhadores e a integridade dos equipamentos. Recomenda-se a continuidade das práticas de monitoramento e manutenção para assegurar a eficácia das medidas implementadas.
Recomendações Finais
Este laudo atesta que, com as adequações realizadas, a organização atende aos requisitos de segurança estabelecidos pela NR 12 e outras normas pertinentes.
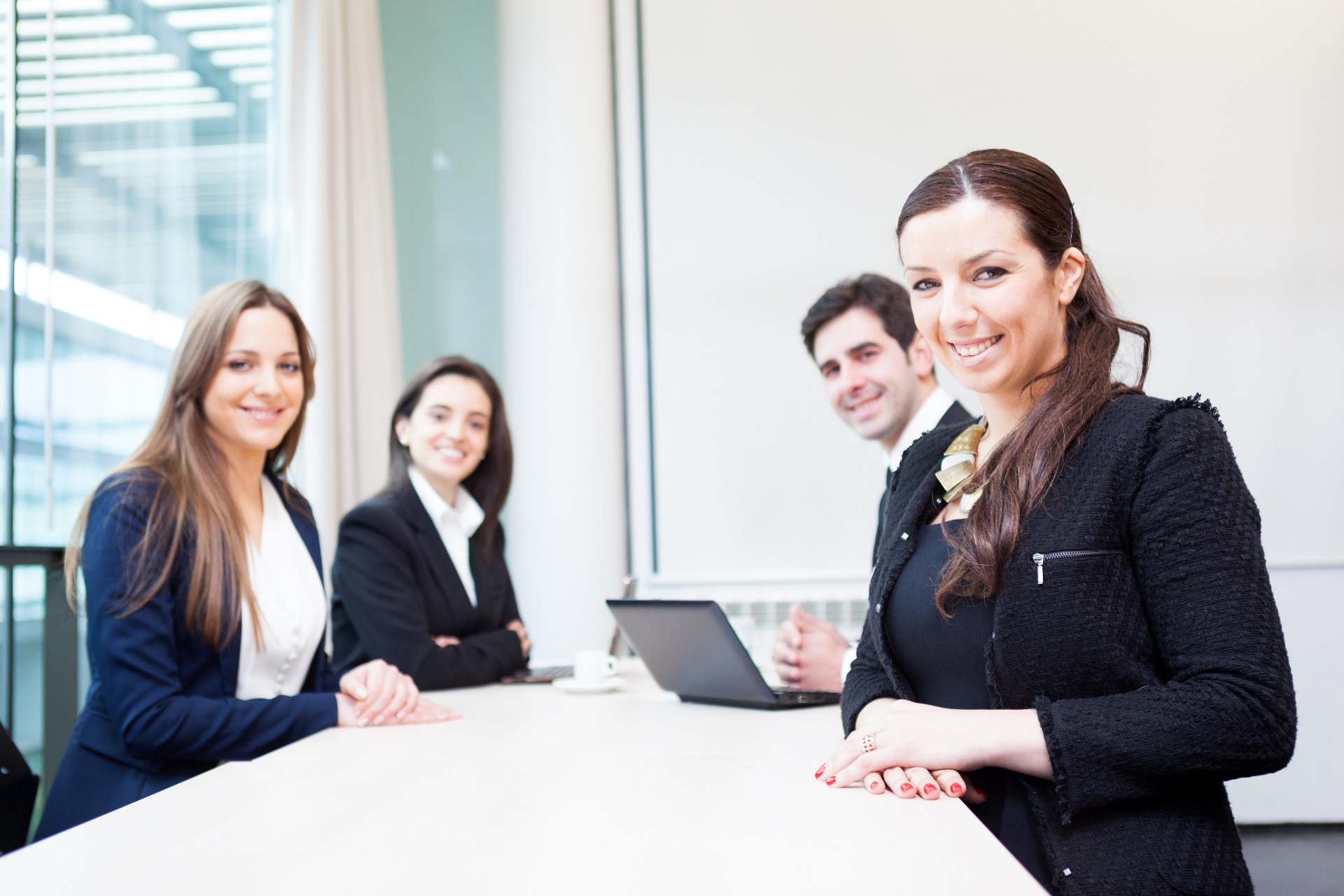
3· Consultoria Especializada
Consultoria Especializada com Certificação CMSE
A adequação de máquinas e equipamentos às normas de segurança é essencial para garantir um ambiente de trabalho seguro e em conformidade com a legislação vigente. A NR 12, que trata da segurança no trabalho em máquinas e equipamentos, é uma das normas técnicas mais importantes nesse contexto. Para ajudar as empresas a se adequarem a essas exigências, a consultoria especializada com certificação CMSE (Certified Machinery Safety Expert) pode ser uma excelente solução.
O que é a Certificação CMSE?
A certificação CMSE (Certified Machinery Safety Expert) é um reconhecimento internacional concedido a profissionais que demonstram conhecimento e habilidade na aplicação de normas de segurança em máquinas. Essa certificação é oferecida pela TÜV NORD e garante que o profissional está capacitado para identificar, avaliar e implementar soluções de segurança eficazes em diferentes tipos de máquinas e equipamentos.
Benefícios da Consultoria com Certificação CMSE
1. Conformidade com a NR 12 e Normas Técnicas
Um consultor certificado CMSE possui conhecimento aprofundado sobre a NR 12 e outras normas técnicas relevantes, garantindo que as soluções propostas estarão em conformidade com a legislação e padrões internacionais.
2. Identificação de Riscos
Os especialistas são treinados para realizar análises de risco detalhadas, identificando possíveis falhas de segurança e propondo melhorias que minimizem riscos de acidentes.
3. Soluções Personalizadas
Cada empresa possui características únicas. Por isso, a consultoria especializada oferece soluções personalizadas, adaptando as recomendações às necessidades específicas de cada cliente.
4. Treinamento e Capacitação
Além de adequar os equipamentos, os consultores podem oferecer treinamentos para capacitar os colaboradores sobre o uso seguro das máquinas, promovendo uma cultura de segurança no ambiente de trabalho.
5. Redução de Custos
A implementação correta de medidas de segurança pode prevenir acidentes, o que reduz custos com indenizações, reparos e paradas não planejadas na produção.
Processo de Adequação
1. Avaliação Inicial
O processo começa com uma avaliação detalhada das máquinas e equipamentos existentes, identificando áreas que não estão em conformidade com a NR 12.
2. Relatório de Conformidade
Após a avaliação, é elaborado um relatório detalhado que descreve todas as inconformidades e as ações necessárias para adequação.
3. Implementação das Medidas
Com base no relatório, são implementadas as medidas corretivas e de segurança, sempre com o acompanhamento do consultor CMSE.
4. Verificação Final
Ao final do processo, é realizada uma verificação para garantir que todas as adequações foram feitas corretamente e que os equipamentos estão seguros para uso.
5. Manutenção e Atualizações
A consultoria também pode incluir planos de manutenção preventiva e atualizações periódicas para assegurar a continuidade da conformidade com a NR 12.
Conclusão
A consultoria especializada com certificação CMSE é um investimento valioso para garantir a segurança no ambiente de trabalho e a conformidade com as normas técnicas. Ao escolher um consultor certificado, as empresas podem ter a tranquilidade de saber que estão em boas mãos, protegendo seus colaboradores e seus ativos.
3· Consultoria Especializada
Consultoria Especializada com Certificação CMSE
A adequação de máquinas e equipamentos às normas de segurança é essencial para garantir um ambiente de trabalho seguro e em conformidade com a legislação vigente. A NR 12, que trata da segurança no trabalho em máquinas e equipamentos, é uma das normas técnicas mais importantes nesse contexto. Para ajudar as empresas a se adequarem a essas exigências, a consultoria especializada com certificação CMSE (Certified Machinery Safety Expert) pode ser uma excelente solução.
O que é a Certificação CMSE?
A certificação CMSE (Certified Machinery Safety Expert) é um reconhecimento internacional concedido a profissionais que demonstram conhecimento e habilidade na aplicação de normas de segurança em máquinas. Essa certificação é oferecida pela TÜV NORD e garante que o profissional está capacitado para identificar, avaliar e implementar soluções de segurança eficazes em diferentes tipos de máquinas e equipamentos.
Benefícios da Consultoria com Certificação CMSE
1. Conformidade com a NR 12 e Normas Técnicas
Um consultor certificado CMSE possui conhecimento aprofundado sobre a NR 12 e outras normas técnicas relevantes, garantindo que as soluções propostas estarão em conformidade com a legislação e padrões internacionais.
2. Identificação de Riscos
Os especialistas são treinados para realizar análises de risco detalhadas, identificando possíveis falhas de segurança e propondo melhorias que minimizem riscos de acidentes.
3. Soluções Personalizadas
Cada empresa possui características únicas. Por isso, a consultoria especializada oferece soluções personalizadas, adaptando as recomendações às necessidades específicas de cada cliente.
4. Treinamento e Capacitação
Além de adequar os equipamentos, os consultores podem oferecer treinamentos para capacitar os colaboradores sobre o uso seguro das máquinas, promovendo uma cultura de segurança no ambiente de trabalho.
5. Redução de Custos
A implementação correta de medidas de segurança pode prevenir acidentes, o que reduz custos com indenizações, reparos e paradas não planejadas na produção.
Processo de Adequação
1. Avaliação Inicial
O processo começa com uma avaliação detalhada das máquinas e equipamentos existentes, identificando áreas que não estão em conformidade com a NR 12.
2. Relatório de Conformidade
Após a avaliação, é elaborado um relatório detalhado que descreve todas as inconformidades e as ações necessárias para adequação.
3. Implementação das Medidas
Com base no relatório, são implementadas as medidas corretivas e de segurança, sempre com o acompanhamento do consultor CMSE.
4. Verificação Final
Ao final do processo, é realizada uma verificação para garantir que todas as adequações foram feitas corretamente e que os equipamentos estão seguros para uso.
5. Manutenção e Atualizações
A consultoria também pode incluir planos de manutenção preventiva e atualizações periódicas para assegurar a continuidade da conformidade com a NR 12.
Conclusão
A consultoria especializada com certificação CMSE é um investimento valioso para garantir a segurança no ambiente de trabalho e a conformidade com as normas técnicas. Ao escolher um consultor certificado, as empresas podem ter a tranquilidade de saber que estão em boas mãos, protegendo seus colaboradores e seus ativos.
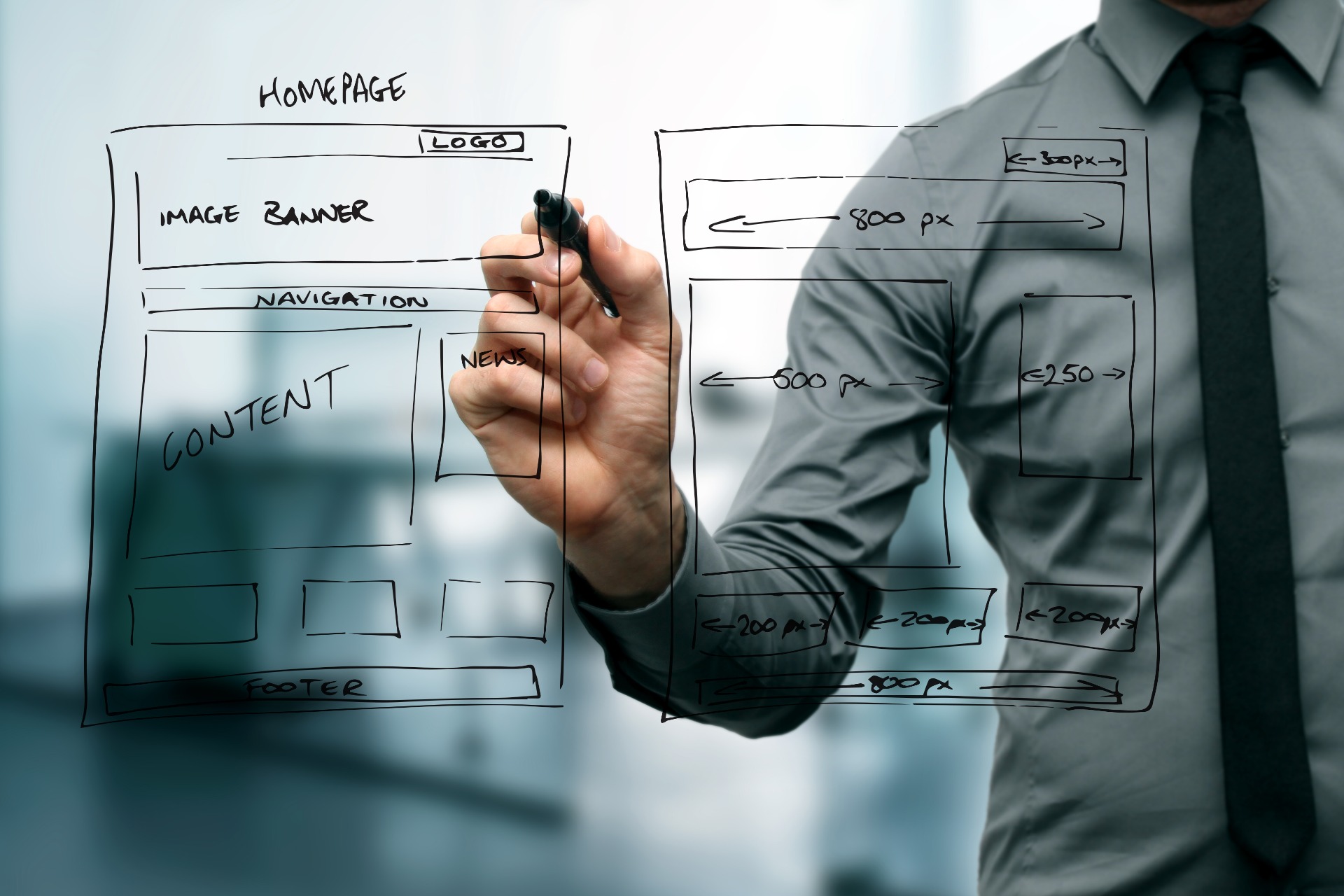
4· Projetos Elétricos
Projetos Elétricos para a Segurança Funcional de Máquinas e Equipamentos
O desenvolvimento de projetos elétricos para máquinas e equipamentos é essencial para garantir a segurança funcional e o atendimento às normas vigentes, como as normas ABNT e NR 12. Estas normas estabelecem critérios específicos para assegurar que as máquinas operem de forma segura, minimizando riscos aos operadores e ao ambiente de trabalho.
Importância da Segurança FuncionalA segurança funcional refere-se à implementação de sistemas de controle que reduzem o risco de falhas que possam causar acidentes. Os projetos elétricos devem incorporar medidas de segurança para evitar incidentes, como curto-circuitos, sobrecargas e mau funcionamento de componentes.
Categorias de Níveis de Desempenho (PLr)As Categorias de Níveis de Desempenho (PLr) são classificações de risco que ajudam a determinar o nível de desempenho necessário para as funções de segurança de uma máquina. Essas categorias são definidas com base na probabilidade de ocorrência, frequência e gravidade de um possível acidente.
Normas ABNT e NR 12Normas ABNT:
As normas da Associação Brasileira de Normas Técnicas (ABNT) estabelecem diretrizes para a segurança e eficiência de instalações elétricas. Elas fornecem um quadro de referência para a concepção e implementação de projetos elétricos, garantindo que os sistemas sejam seguros e funcionais.
Norma Regulamentadora 12 (NR 12)A NR 12 é uma norma brasileira que especifica os requisitos mínimos para a prevenção de acidentes em máquinas e equipamentos. Ela abrange desde a fabricação até a operação, assegurando que todos os aspectos de segurança sejam considerados.
Componentes Chave de um Projeto Elétrico SeguroAnálise de Risco:
Identificação dos potenciais riscos associados às máquinas e equipamentos.
Design Seguro:
Desenvolvimento de sistemas elétricos que incorporem medidas de segurança adequadas.
Implementação de Proteções:
Utilização de dispositivos de proteção, como disjuntores e fusíveis, para prevenir falhas.
Manutenção Preventiva:
Estabelecimento de rotinas de manutenção para garantir que todos os componentes funcionem corretamente e de forma segura.
Treinamento de Operadores:
Capacitação dos operadores para que compreendam os sistemas de segurança e saibam como operar as máquinas de maneira segura.
ConclusãoProjetos elétricos bem elaborados são fundamentais para garantir a segurança funcional de máquinas e equipamentos, conforme as normas ABNT e NR 12. Ao seguir as diretrizes estabelecidas, empresas podem não apenas assegurar a segurança dos operadores, mas também otimizar a eficiência operacional e reduzir custos associados a acidentes e falhas.
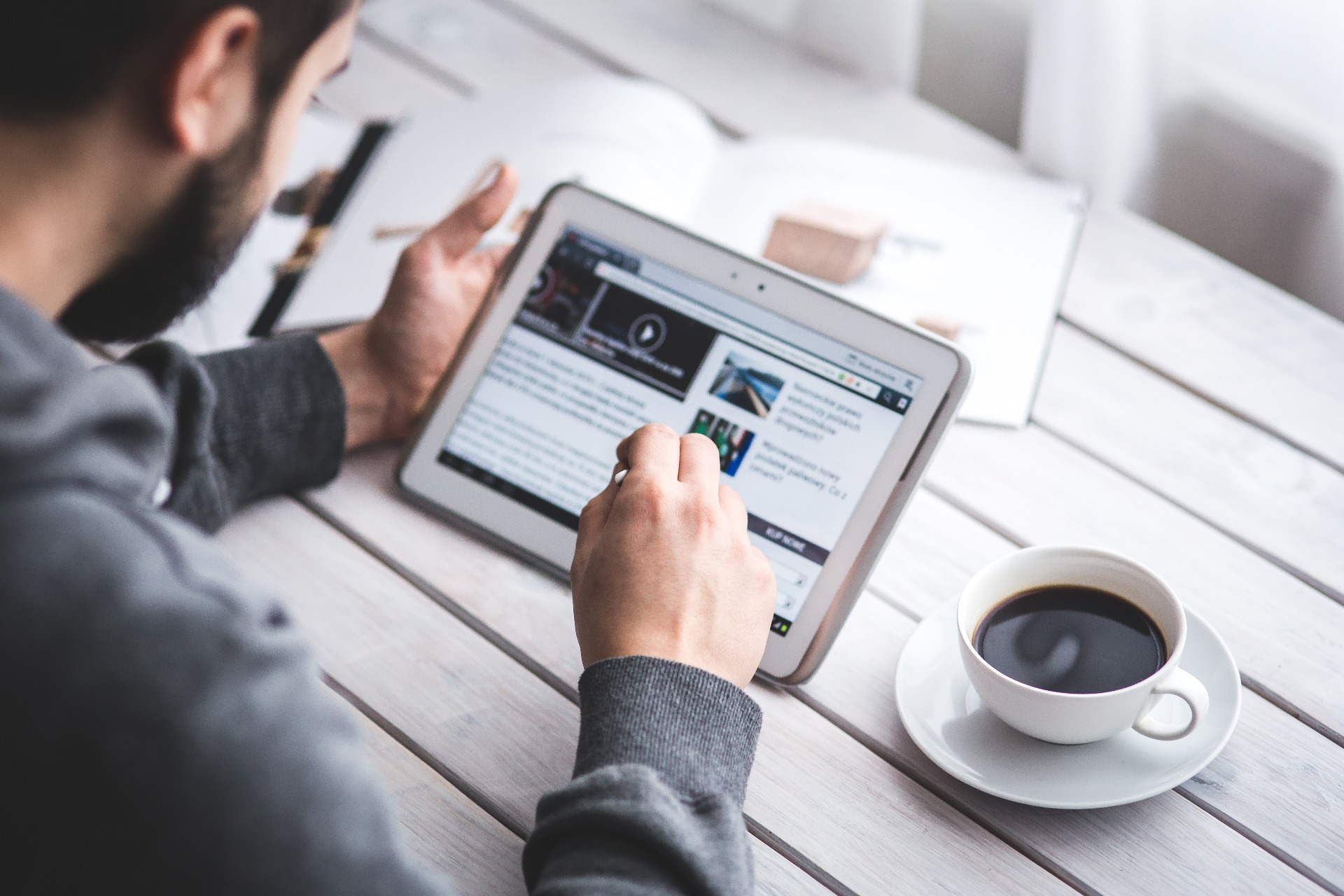
5· Projetos Mecânicos
Proteções Fixas e Móveis para Máquinas
A segurança em ambientes industriais é uma prioridade, e o uso de proteções fixas e móveis em máquinas é essencial para minimizar riscos e garantir a segurança dos trabalhadores. Este texto aborda os principais aspectos dos projetos mecânicos de proteções conforme normas técnicas nacionais e internacionais.
Importância das Proteções
As proteções são barreiras projetadas para prevenir acidentes, evitando o contato direto com partes móveis ou perigosas de máquinas. Elas são cruciais para:
- Prevenir lesões: Reduzem o risco de acidentes como cortes, esmagamentos e amputações.
- Aumentar a produtividade: Ambientes seguros incentivam os trabalhadores e reduzem paradas indesejadas.
- Cumprir requisitos legais: Atender às normas é obrigatório e evita penalidades legais.
Tipos de Proteções
Proteções Fixas
As proteções fixas são estruturas permanentemente montadas em máquinas, que não se movem com as operações normais. Elas são feitas de materiais resistentes e duradouros, como aço ou alumínio.
- Vantagens:
- Alta durabilidade
- Baixa manutenção
- Eficácia na prevenção de acidentes
- Desvantagens:
- Dificuldade de acesso para manutenção
- Possível necessidade de remoção para ajustes
Proteções Móveis
As proteções móveis são partes que se movem ou podem ser removidas para permitir acesso a áreas específicas da máquina durante a manutenção ou operação.
- Vantagens:
- Flexibilidade de uso
- Acesso facilitado para manutenção e ajustes
- Desvantagens:
- Necessidade de dispositivos de segurança adicionais para garantir que a máquina pare quando a proteção é removida
- Maior manutenção devido a partes móveis
Normas Técnicas
Normas Nacionais
No Brasil, as normas da ABNT (Associação Brasileira de Normas Técnicas) são amplamente utilizadas. A NR-12, uma norma regulamentadora, é especialmente relevante para a segurança em máquinas e equipamentos.
Normas Internacionais
As normas ISO (Organização Internacional de Padronização) e a IEC (Comissão Eletrotécnica Internacional) fornecem diretrizes globais. A norma ISO 13857, por exemplo, trata das distâncias de segurança para evitar que partes do corpo entrem em zonas perigosas.
Considerações no Projeto
Para projetar proteções eficazes, é essencial considerar:
- Análise de Risco: Identificar e avaliar perigos potenciais.
- Material: Escolher materiais que ofereçam resistência e durabilidade.
- Acessibilidade: Garantir que as proteções não impeçam o acesso necessário para operações seguras.
- Manutenção: Facilitar a manutenção sem comprometer a segurança.
Conclusão
O design de proteções fixas e móveis é um componente vital para a segurança funcional de máquinas e equipamentos. Seguir normas técnicas e considerar os aspectos de design apropriados assegura um ambiente de trabalho mais seguro e eficiente.
5· Projetos Mecânicos
Proteções Fixas e Móveis para Máquinas
A segurança em ambientes industriais é uma prioridade, e o uso de proteções fixas e móveis em máquinas é essencial para minimizar riscos e garantir a segurança dos trabalhadores. Este texto aborda os principais aspectos dos projetos mecânicos de proteções conforme normas técnicas nacionais e internacionais.
Importância das Proteções
As proteções são barreiras projetadas para prevenir acidentes, evitando o contato direto com partes móveis ou perigosas de máquinas. Elas são cruciais para:
- Prevenir lesões: Reduzem o risco de acidentes como cortes, esmagamentos e amputações.
- Aumentar a produtividade: Ambientes seguros incentivam os trabalhadores e reduzem paradas indesejadas.
- Cumprir requisitos legais: Atender às normas é obrigatório e evita penalidades legais.
Tipos de Proteções
Proteções Fixas
As proteções fixas são estruturas permanentemente montadas em máquinas, que não se movem com as operações normais. Elas são feitas de materiais resistentes e duradouros, como aço ou alumínio.
- Vantagens:
- Alta durabilidade
- Baixa manutenção
- Eficácia na prevenção de acidentes
- Desvantagens:
- Dificuldade de acesso para manutenção
- Possível necessidade de remoção para ajustes
Proteções Móveis
As proteções móveis são partes que se movem ou podem ser removidas para permitir acesso a áreas específicas da máquina durante a manutenção ou operação.
- Vantagens:
- Flexibilidade de uso
- Acesso facilitado para manutenção e ajustes
- Desvantagens:
- Necessidade de dispositivos de segurança adicionais para garantir que a máquina pare quando a proteção é removida
- Maior manutenção devido a partes móveis
Normas Técnicas
Normas Nacionais
No Brasil, as normas da ABNT (Associação Brasileira de Normas Técnicas) são amplamente utilizadas. A NR-12, uma norma regulamentadora, é especialmente relevante para a segurança em máquinas e equipamentos.
Normas Internacionais
As normas ISO (Organização Internacional de Padronização) e a IEC (Comissão Eletrotécnica Internacional) fornecem diretrizes globais. A norma ISO 13857, por exemplo, trata das distâncias de segurança para evitar que partes do corpo entrem em zonas perigosas.
Considerações no Projeto
Para projetar proteções eficazes, é essencial considerar:
- Análise de Risco: Identificar e avaliar perigos potenciais.
- Material: Escolher materiais que ofereçam resistência e durabilidade.
- Acessibilidade: Garantir que as proteções não impeçam o acesso necessário para operações seguras.
- Manutenção: Facilitar a manutenção sem comprometer a segurança.
Conclusão
O design de proteções fixas e móveis é um componente vital para a segurança funcional de máquinas e equipamentos. Seguir normas técnicas e considerar os aspectos de design apropriados assegura um ambiente de trabalho mais seguro e eficiente.
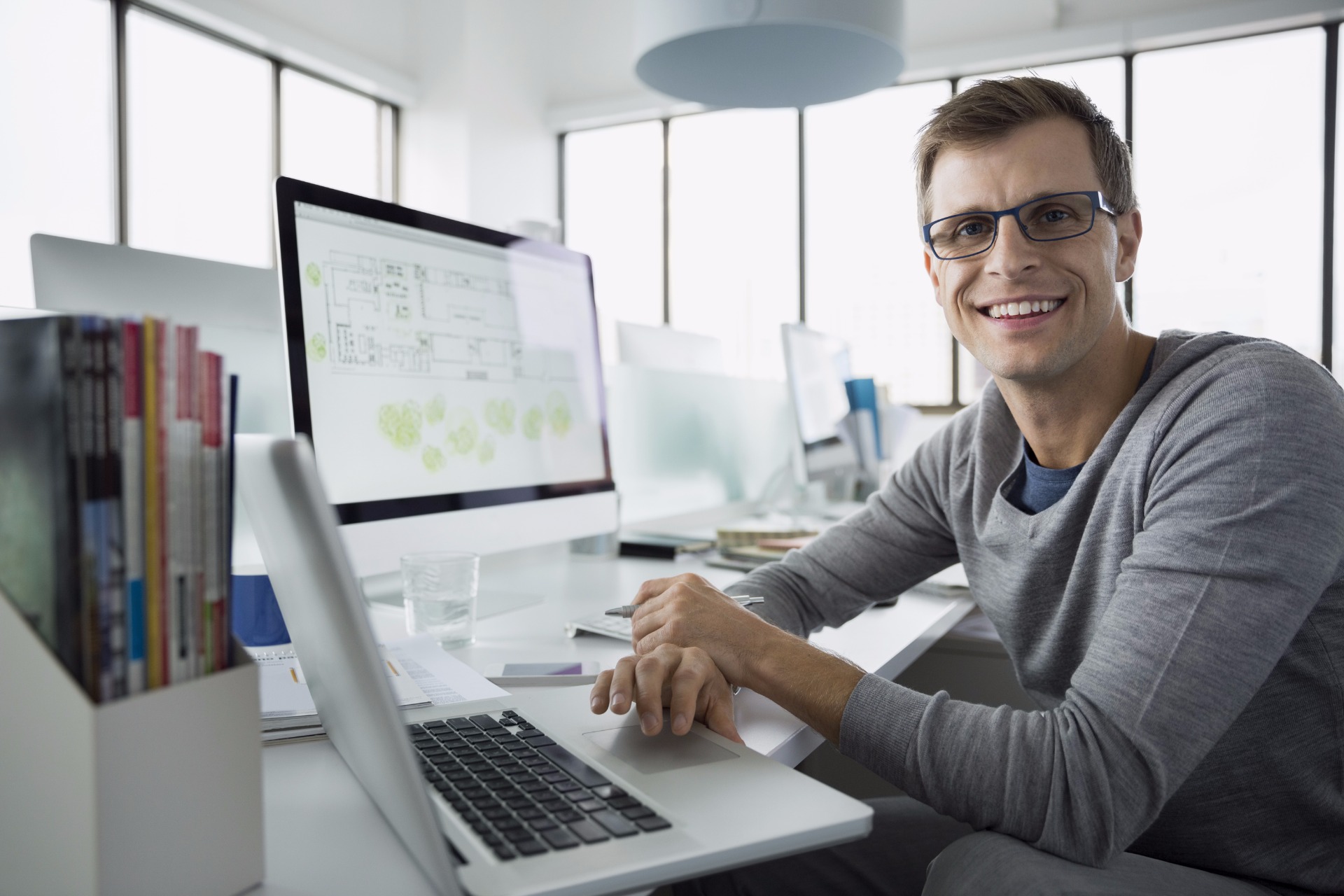
6 · Manuais
Manuais de Instruções para Máquinas e Equipamentos
Os manuais de instruções para máquinas e equipamentos são documentos essenciais que fornecem informações detalhadas sobre o uso, manutenção e segurança dos equipamentos. Eles são fundamentais para garantir que os operadores compreendam todos os aspectos necessários para trabalhar com segurança e eficiência.
Estrutura de um Manual de Instruções
Um manual de instruções geralmente inclui as seguintes seções:
- Introdução: Apresentação do equipamento e seu propósito.
- Especificações Técnicas: Detalhes técnicos, como dimensões, peso, capacidade, e consumo de energia.
- Instruções de Operação: Passo a passo sobre como operar o equipamento de forma segura.
- Manutenção e Cuidados: Diretrizes sobre como realizar a manutenção preventiva e corretiva.
- Soluções de Problemas: Dicas e orientações para solucionar problemas comuns.
- Segurança: Informações sobre práticas de segurança e medidas de precaução.
- Garantia: Termos e condições da garantia do equipamento.
Manuais Reconstituídos para Atender à NR 12
A NR 12 (Norma Regulamentadora nº 12) é uma norma brasileira que estabelece requisitos mínimos para a prevenção de acidentes e doenças do trabalho em máquinas e equipamentos. Ela visa garantir a segurança e saúde dos trabalhadores que operam essas máquinas.
Importância da NR 12
A atualização dos manuais de instrução para atender à NR 12 é crucial, pois:
- Segurança: A NR 12 foca na proteção dos trabalhadores ao exigir que as máquinas sejam seguras.
- Compliance: As empresas devem estar em conformidade com as leis vigentes para evitar multas e sanções.
- Eficiência: Máquinas seguras e bem mantidas tendem a operar de maneira mais eficiente.
Como Reconstituir Manuais para a NR 12
Para que um manual atenda à NR 12, ele deve incluir:
- Análise de Risco: Identificação dos riscos associados ao uso do equipamento e medidas para mitigá-los.
- Medidas de Proteção: Instruções sobre dispositivos de segurança, como barreiras físicas e sistemas de parada de emergência.
- Treinamento: Informações sobre treinamento necessário para operadores e manutenção.
- Procedimentos de Emergência: Orientações claras sobre o que fazer em caso de falhas ou acidentes.
- Documentação Detalhada: Todos os aspectos técnicos e operacionais da máquina devem ser documentados de forma clara.
Benefícios de Manuais Reconstituídos
- Redução de Acidentes: Com informações detalhadas sobre segurança, os riscos de acidentes são significativamente reduzidos.
- Maior Vida Útil do Equipamento: A manutenção adequada, conforme descrito nos manuais, pode prolongar a vida útil das máquinas.
- Melhoria na Produtividade: Operadores bem informados e máquinas seguras contribuem para um ambiente de trabalho mais produtivo.
Os manuais de instruções, quando adequadamente reconstituídos para atender à NR 12, são ferramentas valiosas para promover a segurança e eficiência no ambiente de trabalho. Eles não apenas ajudam a proteger os trabalhadores, mas também asseguram que as máquinas sejam utilizadas de forma otimizada.
6 · Manuais
Manuais de Instruções para Máquinas e Equipamentos
Os manuais de instruções para máquinas e equipamentos são documentos essenciais que fornecem informações detalhadas sobre o uso, manutenção e segurança dos equipamentos. Eles são fundamentais para garantir que os operadores compreendam todos os aspectos necessários para trabalhar com segurança e eficiência.
Estrutura de um Manual de Instruções
Um manual de instruções geralmente inclui as seguintes seções:
- Introdução: Apresentação do equipamento e seu propósito.
- Especificações Técnicas: Detalhes técnicos, como dimensões, peso, capacidade, e consumo de energia.
- Instruções de Operação: Passo a passo sobre como operar o equipamento de forma segura.
- Manutenção e Cuidados: Diretrizes sobre como realizar a manutenção preventiva e corretiva.
- Soluções de Problemas: Dicas e orientações para solucionar problemas comuns.
- Segurança: Informações sobre práticas de segurança e medidas de precaução.
- Garantia: Termos e condições da garantia do equipamento.
Manuais Reconstituídos para Atender à NR 12
A NR 12 (Norma Regulamentadora nº 12) é uma norma brasileira que estabelece requisitos mínimos para a prevenção de acidentes e doenças do trabalho em máquinas e equipamentos. Ela visa garantir a segurança e saúde dos trabalhadores que operam essas máquinas.
Importância da NR 12
A atualização dos manuais de instrução para atender à NR 12 é crucial, pois:
- Segurança: A NR 12 foca na proteção dos trabalhadores ao exigir que as máquinas sejam seguras.
- Compliance: As empresas devem estar em conformidade com as leis vigentes para evitar multas e sanções.
- Eficiência: Máquinas seguras e bem mantidas tendem a operar de maneira mais eficiente.
Como Reconstituir Manuais para a NR 12
Para que um manual atenda à NR 12, ele deve incluir:
- Análise de Risco: Identificação dos riscos associados ao uso do equipamento e medidas para mitigá-los.
- Medidas de Proteção: Instruções sobre dispositivos de segurança, como barreiras físicas e sistemas de parada de emergência.
- Treinamento: Informações sobre treinamento necessário para operadores e manutenção.
- Procedimentos de Emergência: Orientações claras sobre o que fazer em caso de falhas ou acidentes.
- Documentação Detalhada: Todos os aspectos técnicos e operacionais da máquina devem ser documentados de forma clara.
Benefícios de Manuais Reconstituídos
- Redução de Acidentes: Com informações detalhadas sobre segurança, os riscos de acidentes são significativamente reduzidos.
- Maior Vida Útil do Equipamento: A manutenção adequada, conforme descrito nos manuais, pode prolongar a vida útil das máquinas.
- Melhoria na Produtividade: Operadores bem informados e máquinas seguras contribuem para um ambiente de trabalho mais produtivo.
Os manuais de instruções, quando adequadamente reconstituídos para atender à NR 12, são ferramentas valiosas para promover a segurança e eficiência no ambiente de trabalho. Eles não apenas ajudam a proteger os trabalhadores, mas também asseguram que as máquinas sejam utilizadas de forma otimizada.
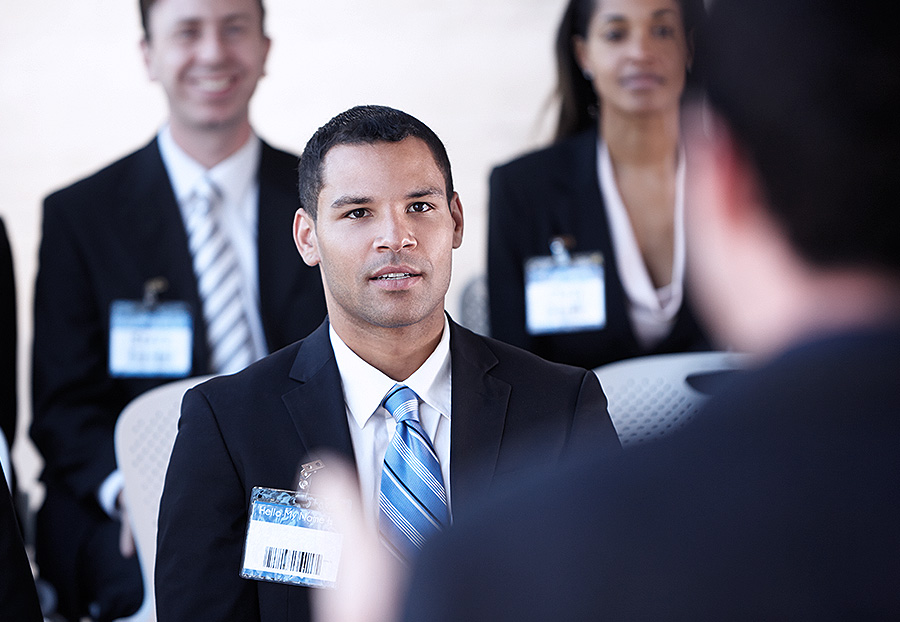
7 · Treinamentos
Treinamentos de Segurança em Máquinas e Equipamentos
A segurança no ambiente de trabalho, especialmente em indústrias que utilizam máquinas e equipamentos, é essencial para a proteção dos trabalhadores. Este guia aborda diferentes aspectos de treinamentos que visam a segurança e a eficiência no manuseio de máquinas, tendo como base a Norma Regulamentadora N° 12 (NR 12) e práticas como LOTO – Lockout / Tagout.
Como Realizar Apreciações de Riscos em Máquinas e Equipamentos
A apreciação de riscos é um processo crucial para identificar, avaliar e controlar os riscos associados ao uso de máquinas e equipamentos. O treinamento deve incluir:
- Identificação de riscos: Avaliar todos os pontos de operação da máquina que podem representar perigo.
- Avaliação de riscos: Determinar a gravidade e a probabilidade de ocorrência de acidentes.
- Controle de riscos: Implementar medidas de controle, como barreiras físicas, sinalizações e procedimentos operacionais seguros.
Norma Regulamentadora N° 12 (NR 12)
A NR 12 estabelece requisitos mínimos para a prevenção de acidentes em máquinas e equipamentos, abrangendo:
- Instalações adequadas: Normas para a instalação correta de máquinas.
- Proteções físicas: Uso de dispositivos de segurança para evitar contato com partes perigosas.
- Sinalização: Instruções claras sobre os riscos e procedimentos de segurança.
Capacitações Conforme NR 12
Os treinamentos devem ser realizados periodicamente para garantir que todos os operadores estejam familiarizados com:
- Funcionamento seguro: Como operar máquinas de forma segura e eficiente.
- Manutenção preventiva: Técnicas para a manutenção regular das máquinas, prevenindo falhas e acidentes.
- Atualizações das normas: Manter-se informado sobre mudanças na regulamentação.
Aplicação de LOTO – Lockout / Tagout
O procedimento LOTO é essencial para garantir que máquinas não sejam ligadas acidentalmente durante a manutenção. O treinamento em LOTO inclui:
- Identificação de fontes de energia: Localizar e identificar todas as fontes de energia que alimentam a máquina.
- Procedimentos de bloqueio: Como aplicar dispositivos de bloqueio para isolar a energia.
- Etiquetagem: Uso de etiquetas de aviso visíveis para alertar sobre o bloqueio.
Outros Treinamentos Relevantes
Além dos aspectos mencionados, outros treinamentos complementares podem incluir:
- Ergonomia: Técnicas para garantir o conforto e a saúde do operador.
- Primeiros socorros: Capacitação para agir rapidamente em caso de acidentes.
- Comunicação efetiva: Treinamento para melhorar a comunicação entre a equipe, especialmente em situações de emergência.
Esses treinamentos são fundamentais para garantir um ambiente de trabalho seguro e eficiente, reduzindo o risco de acidentes e melhorando a produtividade.
7 · Treinamentos
Treinamentos de Segurança em Máquinas e Equipamentos
A segurança no ambiente de trabalho, especialmente em indústrias que utilizam máquinas e equipamentos, é essencial para a proteção dos trabalhadores. Este guia aborda diferentes aspectos de treinamentos que visam a segurança e a eficiência no manuseio de máquinas, tendo como base a Norma Regulamentadora N° 12 (NR 12) e práticas como LOTO – Lockout / Tagout.
Como Realizar Apreciações de Riscos em Máquinas e Equipamentos
A apreciação de riscos é um processo crucial para identificar, avaliar e controlar os riscos associados ao uso de máquinas e equipamentos. O treinamento deve incluir:
- Identificação de riscos: Avaliar todos os pontos de operação da máquina que podem representar perigo.
- Avaliação de riscos: Determinar a gravidade e a probabilidade de ocorrência de acidentes.
- Controle de riscos: Implementar medidas de controle, como barreiras físicas, sinalizações e procedimentos operacionais seguros.
Norma Regulamentadora N° 12 (NR 12)
A NR 12 estabelece requisitos mínimos para a prevenção de acidentes em máquinas e equipamentos, abrangendo:
- Instalações adequadas: Normas para a instalação correta de máquinas.
- Proteções físicas: Uso de dispositivos de segurança para evitar contato com partes perigosas.
- Sinalização: Instruções claras sobre os riscos e procedimentos de segurança.
Capacitações Conforme NR 12
Os treinamentos devem ser realizados periodicamente para garantir que todos os operadores estejam familiarizados com:
- Funcionamento seguro: Como operar máquinas de forma segura e eficiente.
- Manutenção preventiva: Técnicas para a manutenção regular das máquinas, prevenindo falhas e acidentes.
- Atualizações das normas: Manter-se informado sobre mudanças na regulamentação.
Aplicação de LOTO – Lockout / Tagout
O procedimento LOTO é essencial para garantir que máquinas não sejam ligadas acidentalmente durante a manutenção. O treinamento em LOTO inclui:
- Identificação de fontes de energia: Localizar e identificar todas as fontes de energia que alimentam a máquina.
- Procedimentos de bloqueio: Como aplicar dispositivos de bloqueio para isolar a energia.
- Etiquetagem: Uso de etiquetas de aviso visíveis para alertar sobre o bloqueio.
Outros Treinamentos Relevantes
Além dos aspectos mencionados, outros treinamentos complementares podem incluir:
- Ergonomia: Técnicas para garantir o conforto e a saúde do operador.
- Primeiros socorros: Capacitação para agir rapidamente em caso de acidentes.
- Comunicação efetiva: Treinamento para melhorar a comunicação entre a equipe, especialmente em situações de emergência.
Esses treinamentos são fundamentais para garantir um ambiente de trabalho seguro e eficiente, reduzindo o risco de acidentes e melhorando a produtividade.
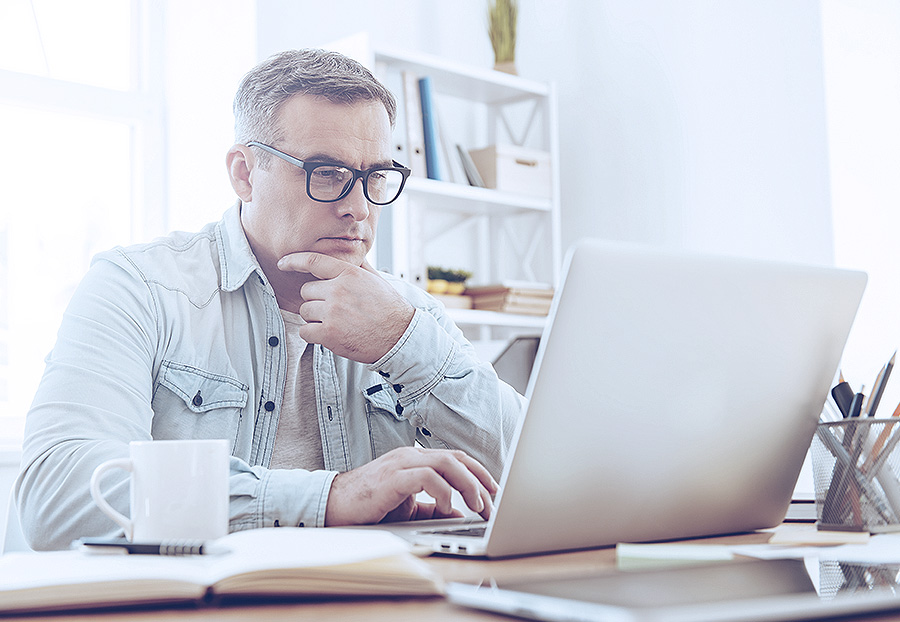
8 · Relatórios de Aterramento de Máquinas e Equipamentos
Relatórios de Aterramentos de Máquinas e Equipamentos
A elaboração de relatórios sobre aterramentos de máquinas e equipamentos, como painéis e invólucros, é essencial para garantir a segurança e o bom funcionamento de instalações elétricas. O aterramento adequado protege contra choques elétricos, incêndios e danos aos equipamentos. Este documento apresenta uma visão geral dos componentes típicos de um relatório de aterramento.
Objetivo do Relatório
O relatório de aterramento tem como objetivo documentar o estado atual do sistema de aterramento de máquinas e equipamentos. Ele deve verificar se o aterramento está conforme as normas técnicas vigentes e identificar possíveis melhorias.
Componentes do Relatório
1. Introdução
- Descrição do Local: Informações gerais sobre a localização física das máquinas e equipamentos.
- Objetivo do Estudo: Explicação sobre a finalidade e a importância do sistema de aterramento na instalação.
2. Normas e Referências
- Normas Aplicáveis: Citar normas nacionais e internacionais que regem os sistemas de aterramento, como a NBR 5410, NBR 5419 e a IEC 60364.
- Referências Técnicas: Incluir estudos e publicações relevantes ao tema.
3. Descrição do Sistema de Aterramento
- Componentes do Sistema: Detalhar os componentes do sistema de aterramento, incluindo hastes, cabos e conexões.
- Malha de Aterramento: Descrever a configuração e o layout da malha de aterramento, com diagramas se possível.
4. Inspeção e Testes Realizados
- Métodos de Inspeção: Relatar os métodos utilizados para inspecionar o sistema de aterramento.
- Testes Realizados: Descrever os testes de resistência de aterramento e continuidade, incluindo a metodologia e os equipamentos utilizados.
- Resultados dos Testes: Apresentar os resultados obtidos e compará-los com os valores de referência.
5. Análise dos Resultados
- Conformidade com Normas: Avaliar se os resultados dos testes estão em conformidade com as normas aplicáveis.
- Identificação de Problemas: Apontar quaisquer problemas ou deficiências encontradas no sistema de aterramento.
6. Recomendações e Melhorias
- Sugestões de Melhorias: Propor ações corretivas ou preventivas para melhorar o sistema de aterramento.
- Plano de Ação: Recomendar um plano de ação para implementar as melhorias sugeridas.
7. Conclusão
- Resumo dos Resultados: Fazer um resumo dos principais achados e conclusões do relatório.
- Importância do Aterramento Efetivo: Reforçar a importância de um sistema de aterramento eficaz para a segurança e proteção de pessoas e equipamentos.
8. Anexos
- Documentação Suplementar: Incluir diagramas, tabelas de dados, certificados de calibração de equipamentos de teste, entre outros documentos relevantes.
Com esses componentes, o relatório de aterramento pode ser um documento abrangente e útil para garantir a segurança e a eficiência das instalações elétricas.
8 · Relatórios de Aterramento de Máquinas e Equipamentos
Relatórios de Aterramentos de Máquinas e Equipamentos
A elaboração de relatórios sobre aterramentos de máquinas e equipamentos, como painéis e invólucros, é essencial para garantir a segurança e o bom funcionamento de instalações elétricas. O aterramento adequado protege contra choques elétricos, incêndios e danos aos equipamentos. Este documento apresenta uma visão geral dos componentes típicos de um relatório de aterramento.
Objetivo do Relatório
O relatório de aterramento tem como objetivo documentar o estado atual do sistema de aterramento de máquinas e equipamentos. Ele deve verificar se o aterramento está conforme as normas técnicas vigentes e identificar possíveis melhorias.
Componentes do Relatório
1. Introdução
- Descrição do Local: Informações gerais sobre a localização física das máquinas e equipamentos.
- Objetivo do Estudo: Explicação sobre a finalidade e a importância do sistema de aterramento na instalação.
2. Normas e Referências
- Normas Aplicáveis: Citar normas nacionais e internacionais que regem os sistemas de aterramento, como a NBR 5410, NBR 5419 e a IEC 60364.
- Referências Técnicas: Incluir estudos e publicações relevantes ao tema.
3. Descrição do Sistema de Aterramento
- Componentes do Sistema: Detalhar os componentes do sistema de aterramento, incluindo hastes, cabos e conexões.
- Malha de Aterramento: Descrever a configuração e o layout da malha de aterramento, com diagramas se possível.
4. Inspeção e Testes Realizados
- Métodos de Inspeção: Relatar os métodos utilizados para inspecionar o sistema de aterramento.
- Testes Realizados: Descrever os testes de resistência de aterramento e continuidade, incluindo a metodologia e os equipamentos utilizados.
- Resultados dos Testes: Apresentar os resultados obtidos e compará-los com os valores de referência.
5. Análise dos Resultados
- Conformidade com Normas: Avaliar se os resultados dos testes estão em conformidade com as normas aplicáveis.
- Identificação de Problemas: Apontar quaisquer problemas ou deficiências encontradas no sistema de aterramento.
6. Recomendações e Melhorias
- Sugestões de Melhorias: Propor ações corretivas ou preventivas para melhorar o sistema de aterramento.
- Plano de Ação: Recomendar um plano de ação para implementar as melhorias sugeridas.
7. Conclusão
- Resumo dos Resultados: Fazer um resumo dos principais achados e conclusões do relatório.
- Importância do Aterramento Efetivo: Reforçar a importância de um sistema de aterramento eficaz para a segurança e proteção de pessoas e equipamentos.
8. Anexos
- Documentação Suplementar: Incluir diagramas, tabelas de dados, certificados de calibração de equipamentos de teste, entre outros documentos relevantes.
Com esses componentes, o relatório de aterramento pode ser um documento abrangente e útil para garantir a segurança e a eficiência das instalações elétricas.
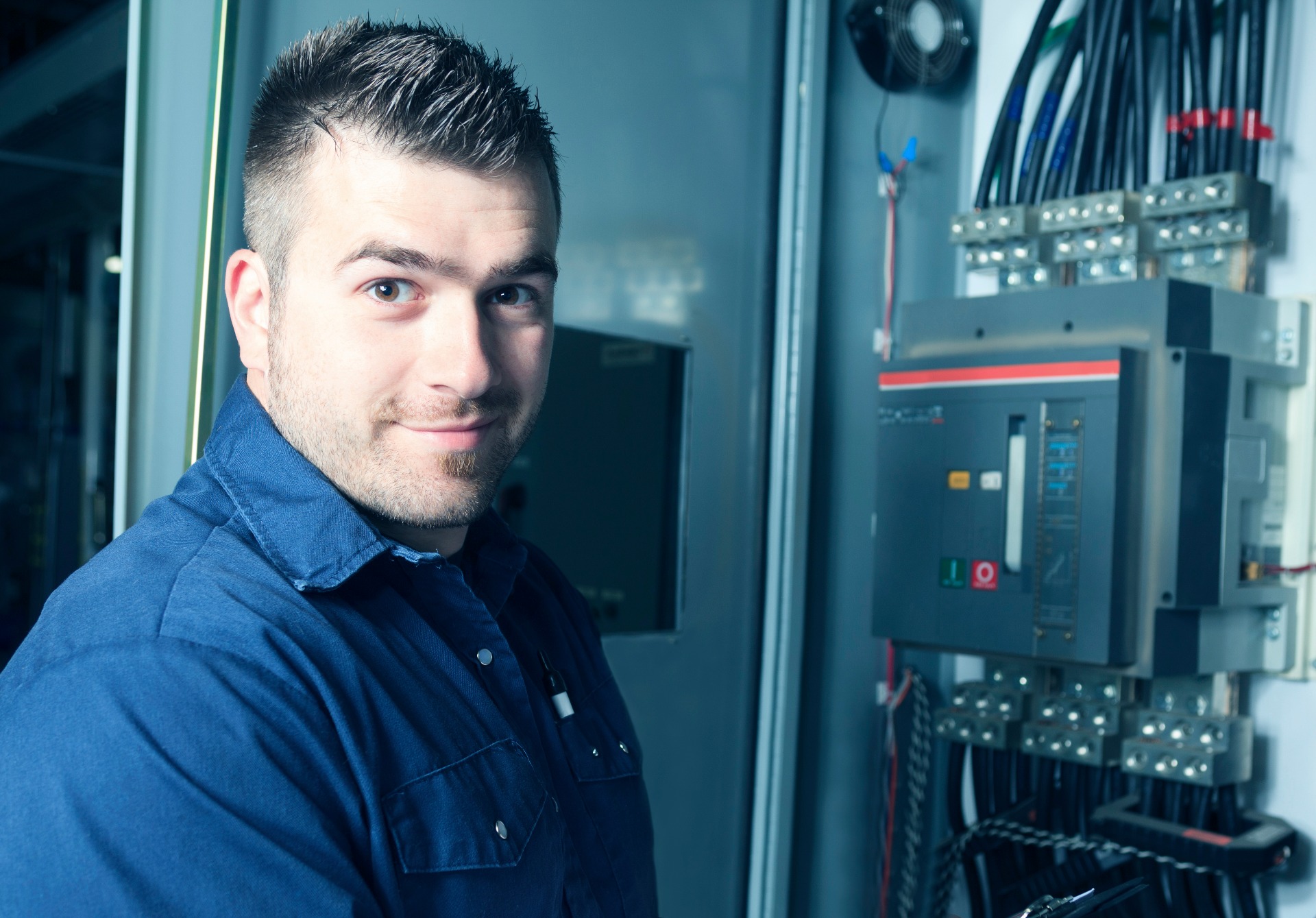
9 · Medições de Arrasto
Medições de Tempo de Parada de Máquinas e Equipamentos
A segurança em ambientes de trabalho que envolvem máquinas e equipamentos é uma prioridade, e as medições de tempo de parada são cruciais para garantir que as operações sejam realizadas de forma segura e eficiente. Conforme o ANEXO I da NR 12, as medições de arrasto têm um papel fundamental na avaliação do desempenho das máquinas. Este documento explora os aspectos importantes dessas medições, além de outras avaliações necessárias para o bom funcionamento dos equipamentos.
Medição de Arrasto
A medição de arrasto refere-se ao tempo necessário para que uma máquina ou equipamento cesse completamente seu movimento após a ativação de um comando de parada. Este tempo é crítico para garantir que operadores e outros trabalhadores estejam seguros durante operações de manutenção ou em caso de emergência.
Importância
- Segurança do operador: Reduz o risco de acidentes ao assegurar que a máquina pare dentro de um tempo seguro.
- Manutenção preventiva: Identifica falhas em sistemas de frenagem que podem precisar de reparos ou ajustes.
- Conformidade legal: Garante que as operações estejam de acordo com as normas regulamentadoras, evitando multas e sanções.
Outras Medições Relevantes
Além das medições de arrasto, há outras avaliações que são essenciais para o monitoramento e segurança de máquinas e equipamentos:
Medição de Velocidade
Monitorar a velocidade de operação das máquinas é vital para garantir que estas operem dentro dos limites seguros e especificados pelo fabricante.
- Prevenção de acidentes: Identifica operações fora dos parâmetros seguros.
- Eficiência operacional: Permite ajustes finos para otimizar o desempenho.
Medição de Posição e Deslocamento
A medição de posição e deslocamento é usada para garantir que as partes móveis das máquinas estejam operando corretamente e dentro dos limites pré-estabelecidos.
- Precisão: Assegura que as máquinas executem suas funções com precisão.
- Evitar colisões: Previne movimentos indesejados que possam resultar em colisões ou danos.
Medição de Escorregamento
O escorregamento refere-se à diferença entre o movimento esperado e o real de uma máquina ou componente. Esta medição é importante para:
- Desempenho: Garante que a máquina funcione eficientemente sem perdas de energia.
- Segurança: Reduz o risco de falhas mecânicas que poderiam causar acidentes.
Implementação das Medições
Para implementar essas medições de forma eficaz, as empresas devem adotar:
- Equipamentos de medição precisos: Investir em tecnologia de medição confiável e calibrada regularmente.
- Treinamento de pessoal: Garantir que os operadores e técnicos sejam treinados adequadamente para realizar e interpretar as medições.
- Manutenção regular: Incorporar as medições como parte de um programa de manutenção preventiva robusto.
Em resumo, as medições de tempo de parada e outras avaliações de desempenho são essenciais para a segurança e eficiência das operações com máquinas e equipamentos. Seguir as diretrizes do ANEXO I da NR 12 não só promove um ambiente de trabalho seguro, mas também assegura a conformidade com as normas regulamentadoras vigentes.
9 · Medições de Arrasto
Medições de Tempo de Parada de Máquinas e Equipamentos
A segurança em ambientes de trabalho que envolvem máquinas e equipamentos é uma prioridade, e as medições de tempo de parada são cruciais para garantir que as operações sejam realizadas de forma segura e eficiente. Conforme o ANEXO I da NR 12, as medições de arrasto têm um papel fundamental na avaliação do desempenho das máquinas. Este documento explora os aspectos importantes dessas medições, além de outras avaliações necessárias para o bom funcionamento dos equipamentos.
Medição de Arrasto
A medição de arrasto refere-se ao tempo necessário para que uma máquina ou equipamento cesse completamente seu movimento após a ativação de um comando de parada. Este tempo é crítico para garantir que operadores e outros trabalhadores estejam seguros durante operações de manutenção ou em caso de emergência.
Importância
- Segurança do operador: Reduz o risco de acidentes ao assegurar que a máquina pare dentro de um tempo seguro.
- Manutenção preventiva: Identifica falhas em sistemas de frenagem que podem precisar de reparos ou ajustes.
- Conformidade legal: Garante que as operações estejam de acordo com as normas regulamentadoras, evitando multas e sanções.
Outras Medições Relevantes
Além das medições de arrasto, há outras avaliações que são essenciais para o monitoramento e segurança de máquinas e equipamentos:
Medição de Velocidade
Monitorar a velocidade de operação das máquinas é vital para garantir que estas operem dentro dos limites seguros e especificados pelo fabricante.
- Prevenção de acidentes: Identifica operações fora dos parâmetros seguros.
- Eficiência operacional: Permite ajustes finos para otimizar o desempenho.
Medição de Posição e Deslocamento
A medição de posição e deslocamento é usada para garantir que as partes móveis das máquinas estejam operando corretamente e dentro dos limites pré-estabelecidos.
- Precisão: Assegura que as máquinas executem suas funções com precisão.
- Evitar colisões: Previne movimentos indesejados que possam resultar em colisões ou danos.
Medição de Escorregamento
O escorregamento refere-se à diferença entre o movimento esperado e o real de uma máquina ou componente. Esta medição é importante para:
- Desempenho: Garante que a máquina funcione eficientemente sem perdas de energia.
- Segurança: Reduz o risco de falhas mecânicas que poderiam causar acidentes.
Implementação das Medições
Para implementar essas medições de forma eficaz, as empresas devem adotar:
- Equipamentos de medição precisos: Investir em tecnologia de medição confiável e calibrada regularmente.
- Treinamento de pessoal: Garantir que os operadores e técnicos sejam treinados adequadamente para realizar e interpretar as medições.
- Manutenção regular: Incorporar as medições como parte de um programa de manutenção preventiva robusto.
Em resumo, as medições de tempo de parada e outras avaliações de desempenho são essenciais para a segurança e eficiência das operações com máquinas e equipamentos. Seguir as diretrizes do ANEXO I da NR 12 não só promove um ambiente de trabalho seguro, mas também assegura a conformidade com as normas regulamentadoras vigentes.
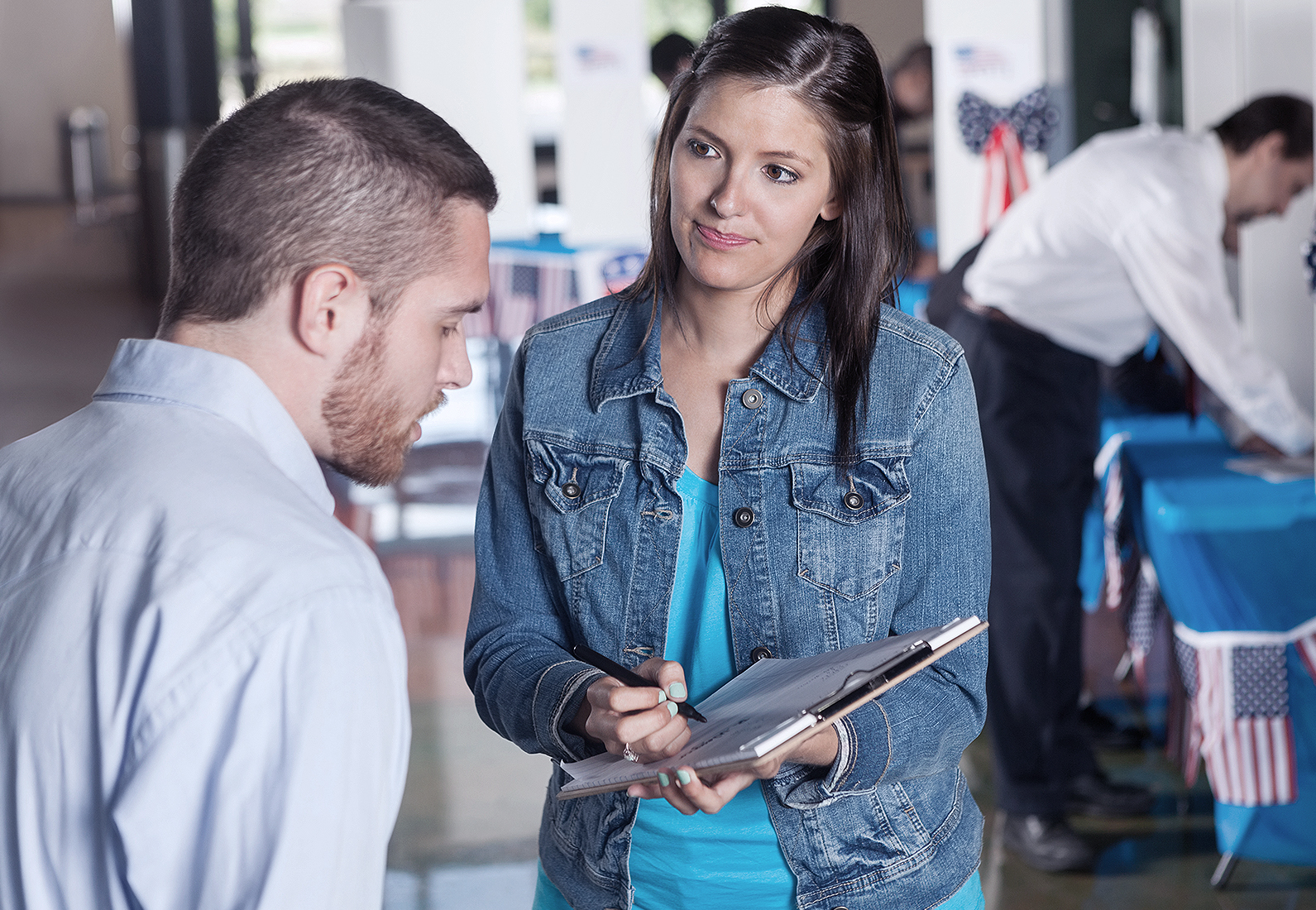
10 · Suporte e acompanhamento de Adequações
Segurança Funcional de Máquinas e Equipamentos
A segurança funcional de máquinas e equipamentos é essencial para garantir um ambiente de trabalho seguro e eficiente. Existem diversos aspectos a serem considerados para alcançar esse objetivo, desde a adequação das máquinas até a documentação e atividades relacionadas. Vamos explorar os principais pontos envolvidos nesse processo.
Suporte e Acompanhamento de Adequações
O suporte e o acompanhamento são fundamentais para garantir que as máquinas e equipamentos estejam adequados às normas de segurança. Algumas das etapas envolvidas incluem:
- Avaliação Inicial: Analisar as condições atuais das máquinas para identificar possíveis riscos e áreas de melhoria.
- Planejamento de Adequações: Desenvolver um plano detalhado de melhorias e adequações necessárias para atender às normas de segurança.
- Implementação das Adequações: Realizar as modificações necessárias, que podem incluir a instalação de dispositivos de segurança, atualização de software, ou alterações estruturais.
- Treinamento de Funcionários: Garantir que todos os operadores e funcionários envolvidos estejam devidamente treinados para utilizar as máquinas com segurança.
Documentos e Atividades Relacionadas à Segurança Funcional
A documentação adequada é crucial para o sucesso de um programa de segurança funcional. Aqui estão alguns dos documentos e atividades frequentemente envolvidos:
- Manuais de Operação: Documentos que descrevem detalhadamente como operar as máquinas de forma segura.
- Relatórios de Inspeção: Registro das inspeções regulares realizadas para garantir que as máquinas continuem em conformidade com as normas de segurança.
- Registros de Manutenção: Documentação de todas as atividades de manutenção realizadas, incluindo detalhes sobre reparos e substituições de peças.
- Análises de Risco: Estudos detalhados que identificam potenciais riscos associados ao uso das máquinas e propõem medidas de mitigação.
Conclusão
Implementar e manter a segurança funcional de máquinas e equipamentos é um processo contínuo que exige atenção cuidadosa e compromisso com a melhoria contínua. Com o suporte adequado e uma abordagem sistemática para a documentação e as atividades relacionadas, é possível criar um ambiente de trabalho mais seguro e eficiente.
10 · Suporte e acompanhamento de Adequações
Segurança Funcional de Máquinas e Equipamentos
A segurança funcional de máquinas e equipamentos é essencial para garantir um ambiente de trabalho seguro e eficiente. Existem diversos aspectos a serem considerados para alcançar esse objetivo, desde a adequação das máquinas até a documentação e atividades relacionadas. Vamos explorar os principais pontos envolvidos nesse processo.
Suporte e Acompanhamento de Adequações
O suporte e o acompanhamento são fundamentais para garantir que as máquinas e equipamentos estejam adequados às normas de segurança. Algumas das etapas envolvidas incluem:
- Avaliação Inicial: Analisar as condições atuais das máquinas para identificar possíveis riscos e áreas de melhoria.
- Planejamento de Adequações: Desenvolver um plano detalhado de melhorias e adequações necessárias para atender às normas de segurança.
- Implementação das Adequações: Realizar as modificações necessárias, que podem incluir a instalação de dispositivos de segurança, atualização de software, ou alterações estruturais.
- Treinamento de Funcionários: Garantir que todos os operadores e funcionários envolvidos estejam devidamente treinados para utilizar as máquinas com segurança.
Documentos e Atividades Relacionadas à Segurança Funcional
A documentação adequada é crucial para o sucesso de um programa de segurança funcional. Aqui estão alguns dos documentos e atividades frequentemente envolvidos:
- Manuais de Operação: Documentos que descrevem detalhadamente como operar as máquinas de forma segura.
- Relatórios de Inspeção: Registro das inspeções regulares realizadas para garantir que as máquinas continuem em conformidade com as normas de segurança.
- Registros de Manutenção: Documentação de todas as atividades de manutenção realizadas, incluindo detalhes sobre reparos e substituições de peças.
- Análises de Risco: Estudos detalhados que identificam potenciais riscos associados ao uso das máquinas e propõem medidas de mitigação.
Conclusão
Implementar e manter a segurança funcional de máquinas e equipamentos é um processo contínuo que exige atenção cuidadosa e compromisso com a melhoria contínua. Com o suporte adequado e uma abordagem sistemática para a documentação e as atividades relacionadas, é possível criar um ambiente de trabalho mais seguro e eficiente.